Fall 2005 Capstone Project: William Olefins
The main objective of this project is to study and refine an existing computer program that was made available to us by Williams Company in Geismar. The computer program is designed to predict the product yield rates and the energy required for the whole process, and it also computes the net profit for the plant.
The current model is directly derived from experimental data by the method of curve fitting (regression type model). However, the predicted outputs from the computer program do not match the actual data for the energy input. Our goal is then to investigate the existing model and find out what causes the program to perform so poorly in predicting the heat input.
This work has been accomplished in four phases.
- Understand and analyze the model.
- Validation of the current model.
- Modify the model to do better predictions.
- Conclusion and recommendations for further studies.
Around mid-semester, the group made a visit to the Williams Olefins Geismar site to tour the facility and discuss our findings with the group's plant liaison, Doug Badon. There it was brought to the attention of the group that our findings were correct but many more developments were needed in order to successfully complete the goal. Mr. Badon discussed to possibility of future topics to focus on. These included fixing a problem with the current Excel model, the fuel flow cost calculations; validating the raw yield equations, steam production, and suction pressure effects used in the model as well as finding a relationship between the oxygen versus fuel.
The Williams Olefins plant in Geismar has 13 furnaces from 2 manufacturers Kellogg and Lummus, denoted ABB and KBR respectively, 10 furnaces are of type ABB, and 3 are of type KBR. The physical model for the material balance is shown below for the ABB furnace with ethane feed stream.
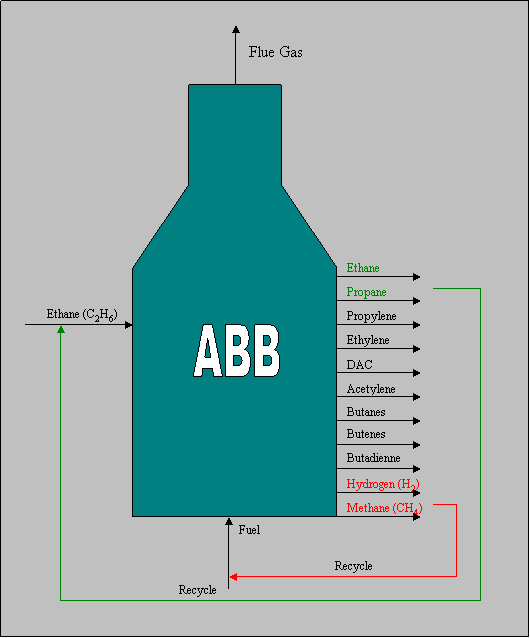
Validation of mass balance
The comparison between the results predicted by the current model and the real data for ethylene production is shown in the following graph. It can be seen from these results that there is good agreement between the mass flow rate of ethylene given by the model and the measured one (actual data). The deviations are even smaller than the margin of error from the data.
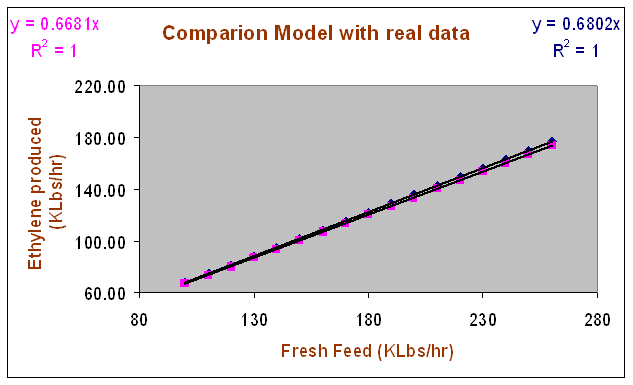
Validation of the energy input.
The comparison between the results predicted by the current model and the real data for energy input is shown in the following graph and table. It can be seen from these results that there is a poor agreement between the energy input given by the model and the measured one (actual data). The deviations are much larger than the margin of error from the data.
This means that the current model should not be used for the prediction of energy input.
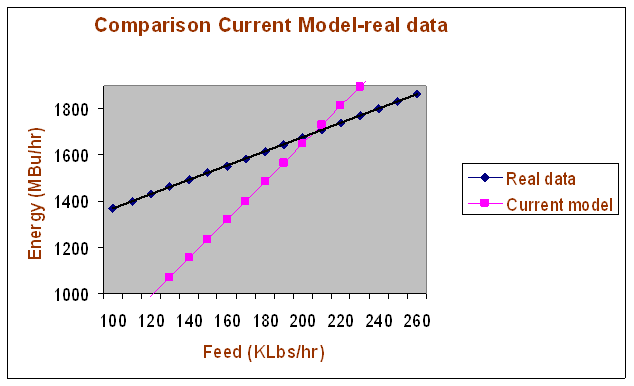
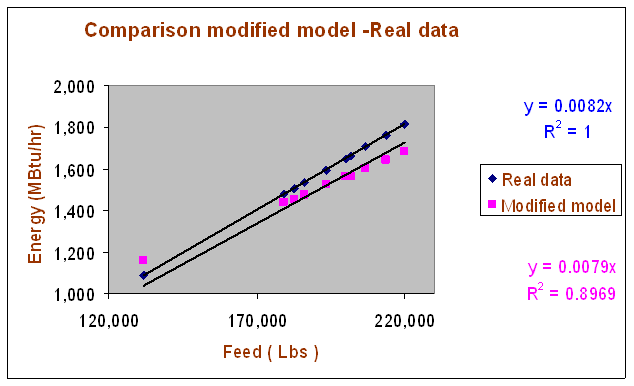
Additional comments
In conclusion, we think that this project gave us an opportunity to deal with a real world problem, in which the building blocks of the chemical industry, ethylene and propylene, are produced through a very complex chemical process called a thermal cracking furnace. In complex problems like these, engineers may sometimes rely on experimental data to develop simple models (regression type model) similar to the one used in this study. However, we should state that the predicted outputs from the computer program will strongly depend on the accuracy and the range of the given data.
Although this model has its limits and assumptions, we still think that the results obtained from this study can help the management team at Williams make reasonable estimations about the optimum operating conditions.
We also believe that there is always room for improvement by taking into account the following steps:
- Study each individual furnace and see if they have the same performance within each group.
- Take into account the chemical composition of the fuel gas.
- Require more accurate data.
- Rewrite the excel program with a more user friendly software such as MATLAB (more convenient to make updates and extensions).